Why Proper DTH Drilling Equipment Maintenance is Crucial
Down-the-hole drilling equipment plays a pivotal role in construction and mining, and it’s essential to ensure that it performs efficiently. Regular maintenance of DTH equipment not only extends the lifespan of your tools but also reduces operational costs and downtime. This ultimate guide covers key strategies for maintaining your DTH hammer, drill bits, air compressor, and more.
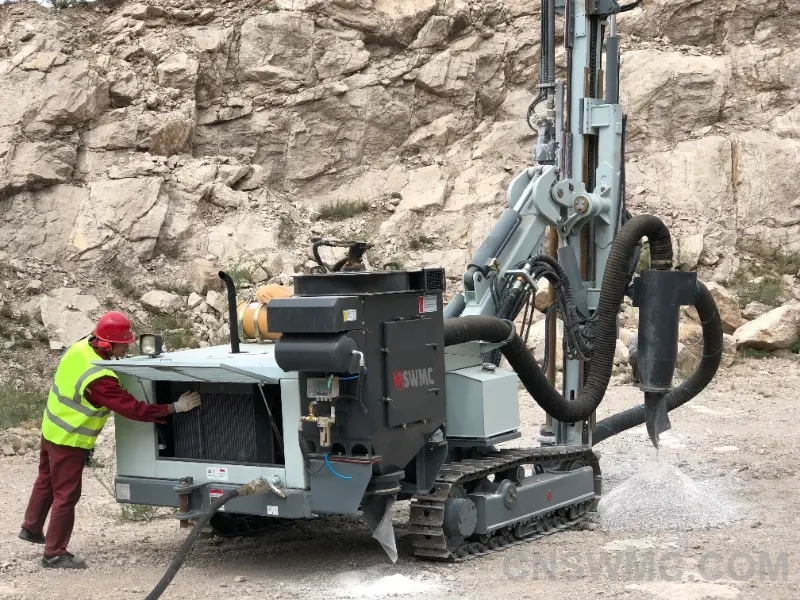
The Importance of Regular Maintenance for DTH Drilling Equipment
If you’re looking for ways to increase the longevity and efficiency of your DTH drilling tools, regular maintenance is key. Preventive maintenance will help you avoid expensive repairs, improve drilling efficiency, and enhance the safety of your operation.
- Improved uptime: Reduced breakdowns mean more time on-site.
- Lower repair costs: Catching problems early saves you money.
- Enhanced safety: Well-maintained equipment ensures a safer work environment.
Key Components of Your DTH Drilling Setup
Before diving into the specifics of maintenance, let’s look at the key components of your DTH drilling system.
1. DTH Hammer
The core of any DTH drilling system. The hammer delivers the high-frequency impacts necessary for breaking rock.
2. Drill Bits
These perform the cutting action. Worn-out bits can reduce efficiency, so timely inspection and replacement are vital.
3. Air Compressor
Powers the hammer and clears debris from the hole. Ensuring it’s in good working condition is essential for performance.
4. Drill Rods
Transmit the force from the hammer. Regular inspection for signs of wear, bending, or corrosion is critical.
5. Rotation Mechanism
While not always included, this adds rotational force for more efficient drilling. Keep it lubricated for better performance.
Essential DTH Drilling Equipment Maintenance Tips
1. Routine Inspections: Catch Problems Early
Regular inspections are the foundation of DTH drilling maintenance. Checking your gear for cracks, leaks, and wear can prevent serious breakdowns.
Key inspection points:
- Hammer: Look for cracks or oil leaks.
- Drill bits: Check for chips, cracks, and wear.
- Rods: Inspect for bending, rust, or excessive wear.
- Air Compressor: Ensure proper air pressure and clear filters.
2. Lubrication: Prevent Friction Damage
Lubrication is essential to reduce friction and wear, helping all parts run smoothly. Applying the right lubricant for DTH equipment can extend the life of your hammer, rods, and bits.
Focus on lubricating these parts:
- Hammer: Follow manufacturer guidelines for optimal oil types.
- Rods and Bits: Regular greasing prevents excessive wear.
- Air Supply System: Keep air filters lubricated to avoid blockage and maintain air pressure.
3. Bit Care: Replace or Sharpen as Needed
Drill bits are often the first to wear out, so keep an eye on their performance. Dull or damaged bits can slow down your operation and increase fuel consumption.
When to replace or sharpen:
- If bits are chipped, cracked, or excessively worn.
- If drilling efficiency is dropping significantly.
4. Air System Care: Ensure Consistent Power
The air system is responsible for powering the DTH hammer and clearing debris. Without it, your drilling operations would be halted.
Key air system maintenance tips:
- Air pressure: Ensure your system is generating the proper PSI.
- Air filters: Clean them regularly to avoid blockages.
- Leaks: Fix any leaks to prevent pressure loss.
5. Proper Storage: Protect Your Gear
Store your DTH tools in a clean, dry environment to prevent rust and corrosion. Proper storage prevents unnecessary damage to your tools and helps them last longer.
Storage best practices:
- Store hammers, rods, and bits in a dry area away from moisture.
- Use protective covers for bits and hammers to avoid impact damage.
6. Professional Servicing: Don’t Skip Expert Help
Although regular checks and DIY maintenance are essential, professional servicing can catch issues you may have missed. Hire experts for periodic servicing to ensure your DTH equipment is running at peak performance.
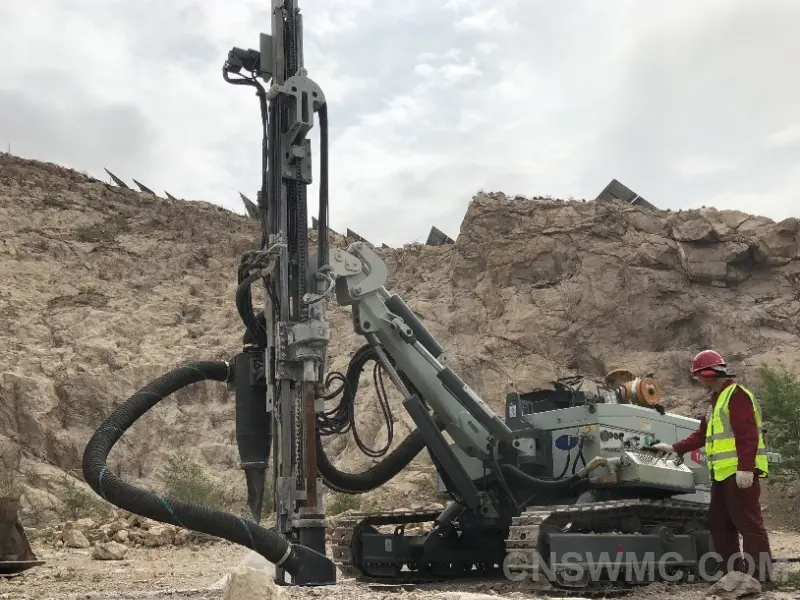
FAQs on DTH Drilling Equipment Maintenance
Q: How often should I check my DTH hammer?
A: Inspect your DTH hammer before and after every project. Pay close attention to any signs of cracks, fluid leaks, or unusual wear.
Q: How do I know when to replace drill bits?
A: Replace drill bits if they are chipped, cracked, or excessively worn down. Also, consider replacing them if drilling performance is reduced.
Q: Can I skip lubrication if I don’t see any wear?
A: No, don’t skip lubrication! It’s a preventive measure that will help extend the life of your equipment and reduce wear.
Q: What should I do if I notice low air pressure?
A: Low air pressure may indicate a clogged filter or a leak. Check and clean the filters, and inspect the air hoses and seals for leaks.
Keep Your DTH Drilling Equipment in Top Shape
Maintaining DTH drilling equipment isn’t difficult, but it’s essential to keep it in optimal condition. By following these simple maintenance tips, you can avoid expensive repairs, extend the life of your gear, and ensure your operations run smoothly.
Implement a regular inspection routine, lubricate key components, and always store your equipment properly. With these practices, your DTH drilling system will serve you efficiently for years to come.